Warehouse Design Solutions: Creating Efficient and Scalable Operations
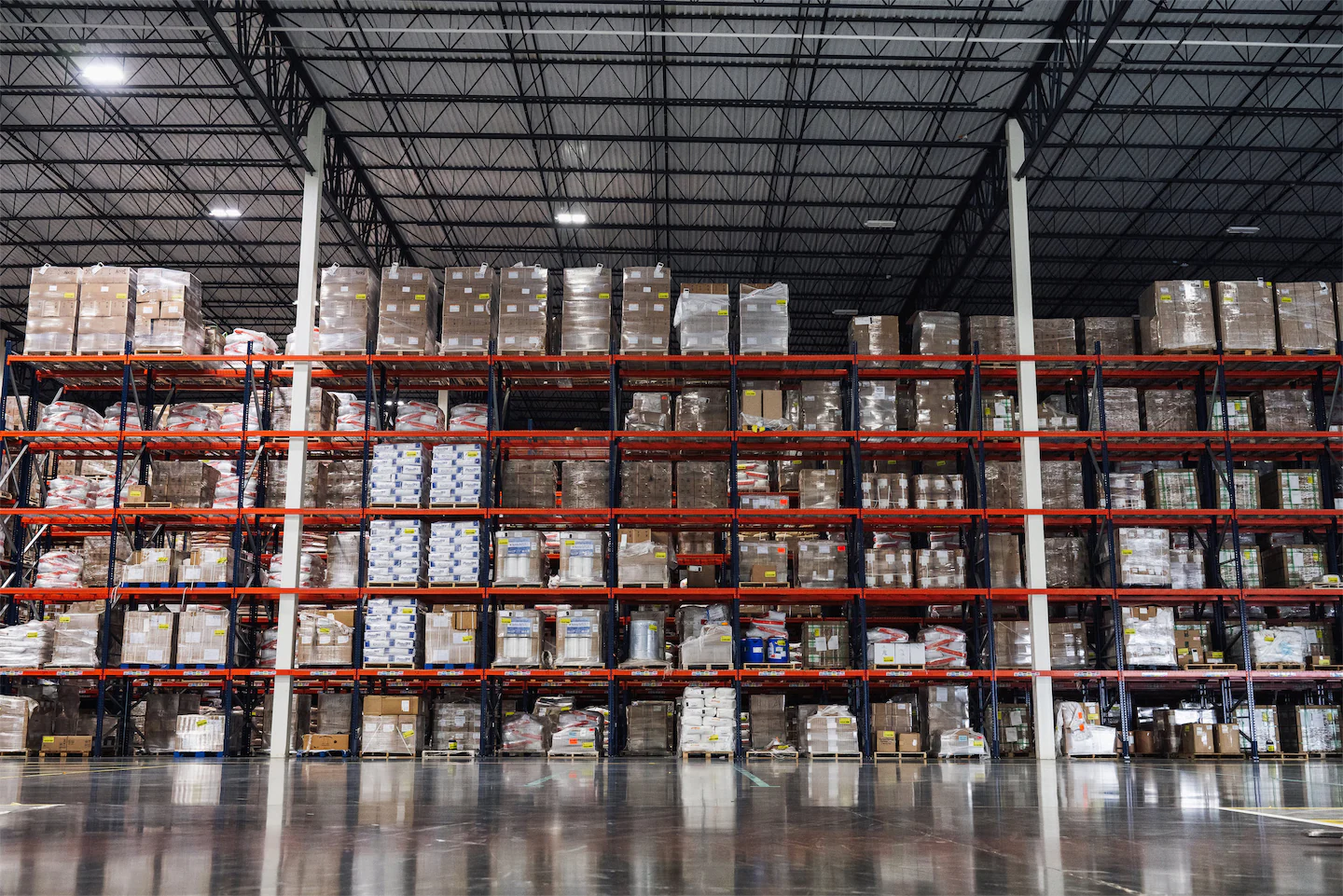
The success of any warehousing operation begins with intelligent facility design. Whether you're planning a new facility or optimizing an existing space, effective warehouse design can dramatically impact operational efficiency, worker safety, and bottom-line results. This guide explores key principles and practical solutions for creating high-performance warehouse operations.
Core principles of effective warehouse design
Successful warehouse design balances multiple competing priorities while maintaining focus on operational efficiency. The most effective facilities begin with a clear understanding of operational requirements, product flow, and future growth needs. This foundational knowledge shapes every aspect of the design process, from basic layout to specific storage solutions.
At its heart, effective warehouse design focuses on two critical elements: workflow optimization and space utilization. Workflow optimization ensures clear movement paths through the facility, efficient product flow from receiving to shipping, and minimal cross-traffic between different operations. Space utilization focuses on maximizing both horizontal and vertical storage capacity while maintaining necessary access and flexibility for future changes.
Understanding workflow and space requirements
Before diving into specific design elements, understanding your operation's unique workflow patterns proves crucial. This begins with a detailed analysis of current or projected operations, examining everything from receiving patterns to shipping volumes. Product characteristics, order profiles, seasonal variations, and equipment requirements all play vital roles in determining optimal facility layout.
The movement of goods through a facility follows distinct patterns, and successful warehouse design aligns with these natural flows. Consider how products move from receiving to storage, from storage to picking, and finally to shipping. Each transition point presents opportunities for either efficiency or bottlenecks, making it essential to carefully plan these critical areas.
Optimizing vertical space utilization
Modern warehouse design increasingly focuses on maximizing vertical space utilization. With rising real estate costs and growing storage demands, making effective use of available height can significantly improve storage density and operational efficiency. However, the push toward higher storage must balance with practical considerations of access and safety.
Successful vertical storage strategies consider multiple factors beyond simple maximum height. Equipment capabilities, product characteristics, picking frequency, and safety requirements all influence optimal storage height. While high-bay racking might maximize storage density, it might not provide the most efficient solution for frequently accessed items or operations with high product turnover.
Designing efficient picking operations
Order picking typically represents the largest labor component in warehouse operations. Effective facility design can dramatically impact picking efficiency through thoughtful zone configuration, equipment selection, and storage layout. The goal is to minimize travel time and maximize picking accuracy while maintaining flexible operations that can adapt to changing requirements.
Modern picking operations often combine multiple strategies based on order profiles and product characteristics. Fast-moving items might occupy easily accessible ground-level locations, while slower-moving stock could be stored in higher locations or more distant zones. The key lies in matching storage locations and picking methods to actual order patterns and operational requirements.
Equipment considerations in facility design
Material handling equipment selection significantly impacts warehouse design requirements. From basic lift trucks to automated systems, equipment choices influence everything from aisle widths to floor specifications. These choices must balance immediate operational needs with potential future requirements, ensuring the facility can adapt as operations evolve.
Consider not just the equipment itself, but also supporting infrastructure requirements. Charging stations, maintenance areas, and equipment staging zones all require appropriate space allocation. Additionally, future automation possibilities might necessitate specific floor flatness requirements or power distribution capabilities.
Dock and staging area design
Loading dock design plays a crucial role in maintaining efficient product flow through the facility. Proper dock design extends beyond simple truck access to encompass staging areas, traffic patterns, and worker safety considerations. The most effective dock areas provide adequate space for both inbound and outbound operations while maintaining clear separation between different activities.
Successful dock design begins with a thorough understanding of shipping and receiving patterns. The number of doors, their configuration, and associated staging areas should align with expected volumes and timing patterns. Consider both current requirements and potential future needs, as dock capacity often proves difficult to modify once established.
Storage systems and solutions
Modern warehouses benefit from a wide range of storage solutions, each offering different advantages for specific applications. From traditional pallet racking to automated storage systems, selecting the right solutions proves crucial for operational success. The key lies in matching storage systems to actual operational requirements while maintaining flexibility for future changes.
When evaluating storage solutions, consider not just current needs but also potential future requirements. Storage systems represent a significant investment and can be difficult to modify once installed. The most successful designs incorporate flexibility to accommodate changing product mixes and operational requirements.
Technology infrastructure planning
Modern warehouses rely heavily on technology for efficient operations. Facility design must include appropriate infrastructure to support both current and future technology needs. This includes everything from basic power distribution to advanced automation systems. Planning should anticipate future requirements while providing flexibility for technological evolution.
Successful technology integration requires careful consideration of physical infrastructure requirements. Network connectivity, power distribution, and equipment interfaces all need appropriate planning and implementation. Additionally, consider future technology adoption possibilities and ensure the facility can accommodate potential upgrades or modifications.
Implementation and optimization
Implementing a new warehouse design requires careful planning and execution. Success depends on thorough preparation, clear communication, and careful attention to detail during the implementation phase. The process should include clear timelines, responsibility assignments, and success metrics to ensure effective execution.
Most importantly, recognize that initial implementation represents just the beginning. Continuous monitoring and optimization help ensure the facility maintains peak efficiency as operations evolve. Regular assessment of performance metrics and operational requirements allows for ongoing improvements and adjustments as needed.
Ready to optimize your warehouse design? Contact our team to learn how we can help create an efficient, scalable solution for your operations.
Understanding workflow and space requirements
Before diving into specific design elements, understanding your operation's unique workflow patterns proves crucial. This begins with a detailed analysis of current or projected operations, including receiving patterns, storage requirements, picking operations, and shipping volumes.
Consider factors such as:
- Product characteristics and storage requirements
- Order profiles and picking patterns
- Seasonal variations in volume
- Equipment requirements and constraints
- Labor requirements and movement patterns
This analysis forms the foundation for all subsequent design decisions, ensuring that the final layout supports efficient operations while maintaining flexibility for future changes.
Optimizing vertical space utilization
Modern warehouse design increasingly focuses on maximizing vertical space utilization. With rising real estate costs and growing storage demands, making effective use of available height can significantly improve storage density and operational efficiency.
Vertical storage solutions must balance accessibility with storage density. While pushing racking heights higher increases storage capacity, it can also impact picking efficiency and equipment requirements. Successful designs find the right balance for each operation's specific needs.
Designing efficient picking operations
Order picking typically represents the largest labor component in warehouse operations. Effective facility design can dramatically impact picking efficiency through proper zone configuration, equipment selection, and storage layout.
Modern picking operations often combine multiple strategies based on order profiles and product characteristics. From basic manual picking to sophisticated automation systems, the key lies in matching the design to actual operational requirements while maintaining flexibility for volume fluctuations.
Equipment considerations in facility design
The type of material handling equipment used in a facility significantly impacts design requirements. From aisle widths to floor specifications, equipment choices influence numerous aspects of warehouse layout and infrastructure.
When selecting equipment and designing appropriate spaces, consider:
- Lift truck turning radiuses
- Load sizes and weights
- Power source requirements
- Maintenance access needs
- Future automation possibilities
Dock and staging area design
Loading dock design plays a crucial role in maintaining efficient product flow through the facility. Proper dock design considers factors beyond simple truck access, incorporating staging areas, material flow patterns, and worker safety considerations.
Effective dock areas provide adequate space for staging both inbound and outbound shipments while maintaining clear traffic patterns. The number of dock doors, their configuration, and associated staging areas should align with expected shipping volumes and patterns.
Storage systems and racking solutions
Modern warehouses benefit from a wide range of storage solutions, each offering different advantages for specific applications. From traditional pallet racking to automated storage and retrieval systems, selecting the right storage solutions proves crucial for operational success.
Key considerations in storage system selection include:
- Product characteristics
- Throughput requirements
- Access needs
- Space utilization
- Cost considerations
- Future flexibility
Automation integration considerations
While not every facility requires extensive automation, designing with future automation possibilities in mind can prevent costly modifications later. This includes considering power requirements, floor flatness specifications, and space for potential automation systems.
Even facilities that initially operate manually can benefit from "automation-ready" design elements that facilitate future technology integration. This might include appropriate ceiling heights, column spacing, and infrastructure capacity to support future automation needs.
Safety and compliance in design
Safety considerations must be integrated into every aspect of warehouse design, from traffic patterns to emergency access. Proper design creates clear separation between pedestrian and vehicle traffic while ensuring adequate access for emergency response.
Essential safety design elements include:
- Clearly marked traffic lanes
- Adequate lighting throughout
- Emergency exit access
- Fire suppression systems
- Ventilation requirements
- Safety equipment placement
Environmental considerations
Modern warehouse design increasingly incorporates environmental considerations, both for sustainability and operational efficiency. From natural lighting to energy-efficient systems, these elements can significantly impact both operating costs and environmental footprint.
Sustainable design elements often include:
- Energy-efficient lighting systems
- Natural light utilization
- High-efficiency HVAC systems
- Solar power readiness
- Water conservation features
- Sustainable building materials
Technology infrastructure planning
Modern warehouses rely heavily on technology for efficient operations. Facility design must include appropriate infrastructure to support both current and future technology needs, from wireless networks to automation systems.
Infrastructure considerations should include:
- Network connectivity throughout
- Power distribution requirements
- Equipment charging stations
- Data center space
- Security system integration
- Future technology accommodation
Flexible design for future adaptation
Perhaps the most crucial aspect of warehouse design is building in flexibility for future changes. Business needs evolve, technology advances, and operational requirements change. Successful facility designs accommodate these changes without requiring major modifications.
Implementation and optimization
Implementing a new warehouse design or modification requires careful planning and execution. Success depends on thorough preparation, clear communication, and careful attention to detail during the implementation phase.
Key steps in the implementation process include:
- Detailed project planning
- Stakeholder communication
- Phased implementation strategy
- Training and documentation
- Performance monitoring
- Continuous improvement processes
Measuring design success
Effective warehouse design ultimately proves its value through improved operational performance. Establishing clear metrics for success and monitoring these indicators helps ensure that design choices deliver expected benefits while identifying areas for future improvement.
Ready to optimize your warehouse design? Contact our team to learn how we can help create an efficient, scalable solution for your operations.
Recent blogs
.webp)
Commonwealth Warehouse Wins ADM's 2023 Value in Excellence Award
Commonwealth Warehouse Inc. has been honored with ADM's prestigious 2023 Value in Excellence Award, recognizing outstanding performance in delivering logistics solutions. This recognition from ADM, a global leader in sustainable sourced solutions, highlights Commonwealth's commitment to exceptional service and innovation in the logistics industry.
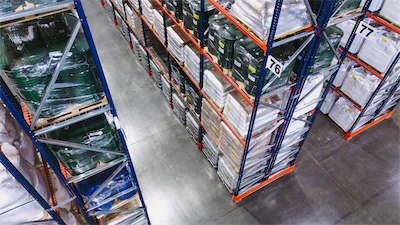
Chemical Logistics and Warehousing: A Guide to Safe and Efficient Operations
Chemical logistics presents unique challenges that demand specialized knowledge, rigorous safety protocols, and unwavering attention to detail. From handling hazardous materials to maintaining precise environmental controls, successful chemical warehousing requires a comprehensive understanding of both operational requirements and safety regulations.
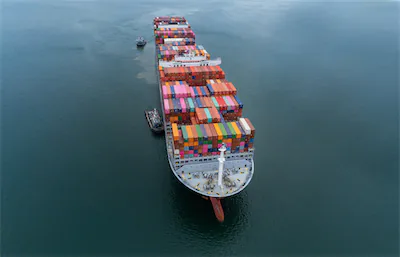
Transportation Logistics: A Guide to Multimodal Shipping Solutions
In today's complex supply chain environment, successful transportation logistics requires more than simply moving goods from point A to point B. Modern shipping demands a sophisticated approach that leverages multiple transportation modes, advanced planning tools, and strategic partnerships to optimize both efficiency and cost-effectiveness.
Arrange a visit
See the Commonwealth difference in action
We believe the best way to understand our capabilities is to experience them firsthand. We invite you to tour one of our facilities, meet our team, and discover how Commonwealth can optimize your logistics operations. Let us show you why so many businesses trust us with their supply chain needs.